Plasma cutting is one of the advanced technologies in the field of metal cutting, widely used across various industries due to its high speed and ability to cut different materials, particularly conductive metals. In this article, we will explore the details of this method, its operation, advantages, disadvantages, and applications.
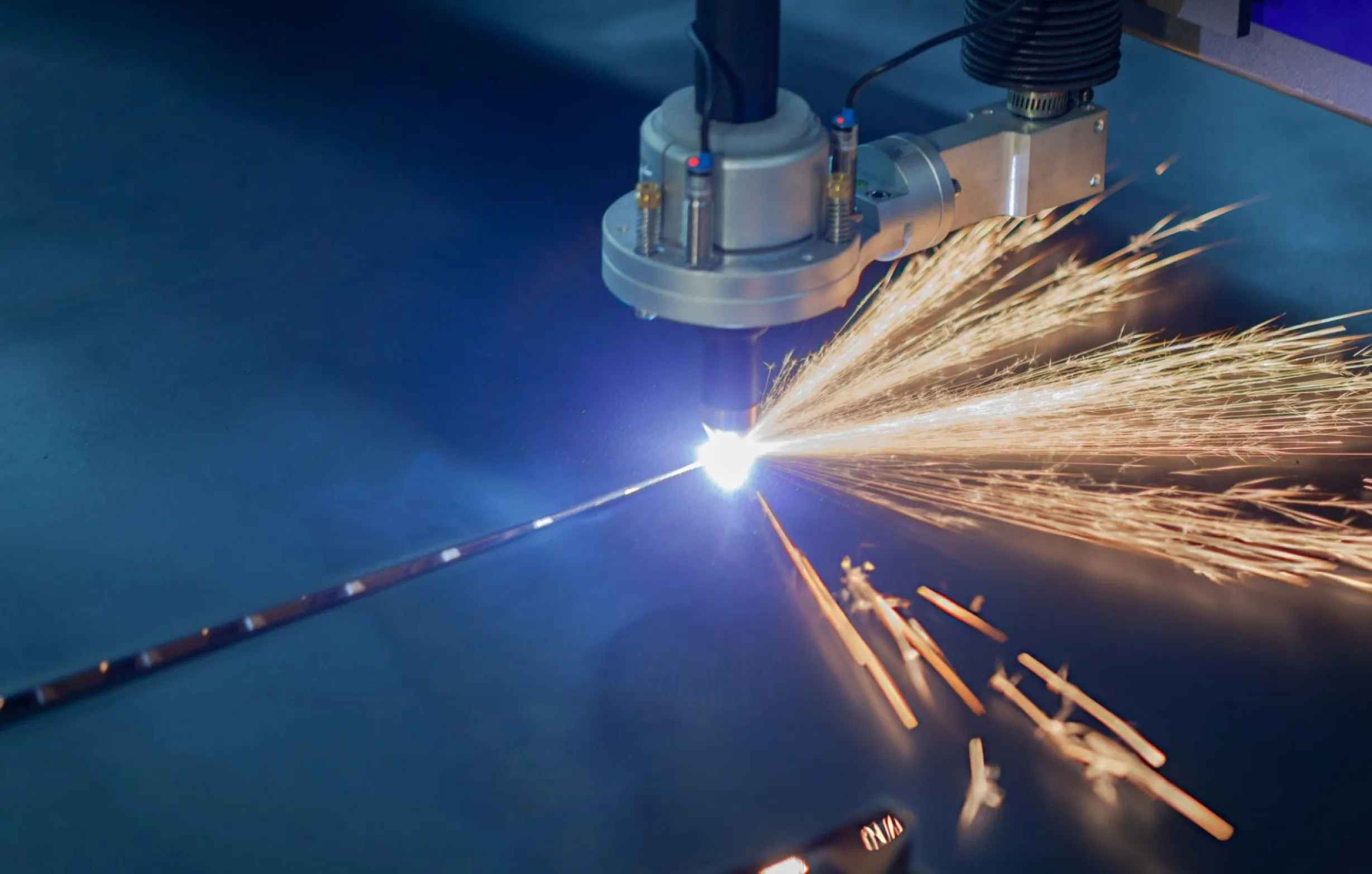
Detailed Examination of the Plasma Cutting Method
Category:
Publication Date: 2025/01/17
What You Will Read in This Article
How Plasma Cutting Works
Plasma cutting uses a jet of ionized gas, heated to an extremely high temperature, to cut metals. This process includes the following steps:
- Input Gas: High-pressure gas (such as air, nitrogen, or oxygen) is expelled through the machine’s nozzle
- Electric Arc Formation: An electric arc is generated between the gas and the metal surface, dramatically increasing the gas temperature and converting it into a plasma state.
- Metal cutting: High-temperature plasma melts the metal at the cutting point, and high-pressure gas expels the molten metal from the cutting area.
Advantages of plasma cutting
- High speed: Plasma cutting is very fast, especially for light to medium-thick metals, making it suitable for mass production.
- Flexibility: This method can cut various metals, including steel, aluminum, and copper, with high precision.
- Lower cost than laser: Compared to laser cutting, plasma cutting equipment has a lower initial cost, but still offers high accuracy and quality.
Disadvantages of plasma cutting
- Lower edge quality than laser: Plasma-cut edges may require secondary operations such as smoothing or grinding.
- Thickness limitation: This method is not suitable for very thick metals (more than 50 mm).
- Noise and harmful fumes: Plasma cutting can produce a lot of noise and fumes, which requires proper ventilation and the use of safety equipment.
Applications of plasma cutting
- Automotive industry: For the production of automotive parts such as chassis and body parts.
- Construction: Cutting beams, metal sheets, and steel structures.
- Shipbuilding industry: Cutting thick steel sheets to build ship hulls.
- Industrial equipment production: Cutting metal parts for machinery and factory equipment.
conclusion
Plasma cutting is an efficient and cost-effective method for cutting conductive metals with high precision and speed. This technology is especially ideal for applications that require fast cutting and mass production. However, limitations such as edge quality and cuttable thickness must be considered when choosing this method.
Related Articles