One of the critical stages in die casting is injecting molten metal into the mold. This phase requires high precision to ensure the final part meets quality standards. Below, we examine this step in greater detail.
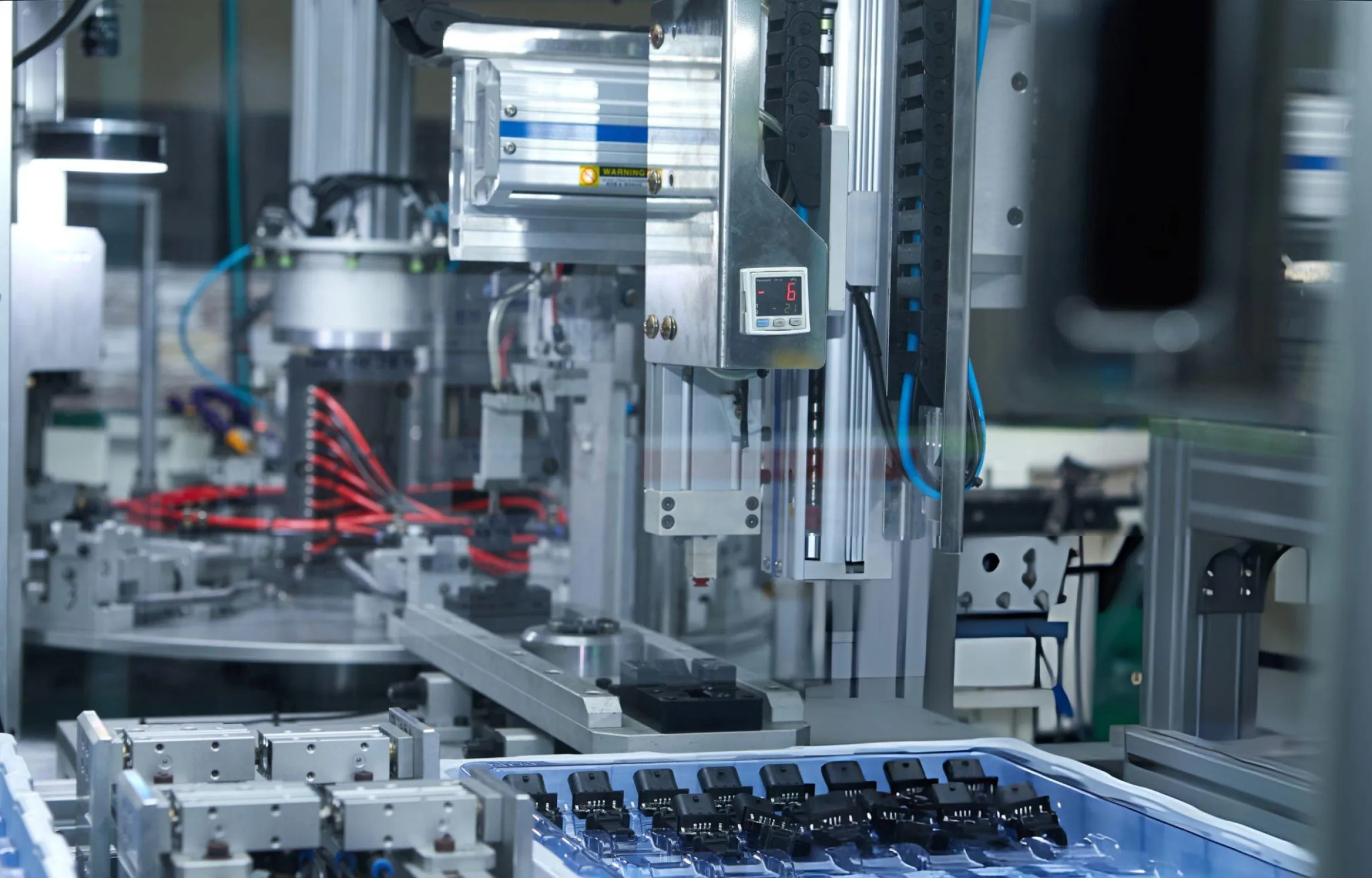
Analysis of Metal Injection Process in Die Casting
1. Molten Metal Preparation
Prior to injection, the base metal (typically aluminum, zinc, or magnesium) is melted in specialized furnaces. The molten metal temperature must be precisely controlled to achieve optimal viscosity for injection. Improper temperatures (either excessive or insufficient) can lead to casting defects such as:
✔ Gas porosity (air entrapment)
✔ Surface cracks (hot tearing)
✔ Incomplete filling (cold shuts)
2. Molten Metal Injection
Following preparation, the molten metal is transferred into the injection system. This system features a hydraulic plunger that forcibly drives the metal into the die cavity under high pressure (typically 500–1500 bar). The intense pressure ensures:
✔ Complete cavity filling, including intricate geometries
✔ Reduced porosity through minimized air entrapment
✔ Fine surface finish (Ra 1.6–3.2 μm achievable)
- Injection Pressure: Depending on the type of metal and the complexity of the part, injection pressure typically ranges between 10 and 175 megapascals. Higher pressure is used for more complex parts with thinner walls to ensure that all sections of the mold are fully filled.
- Injection Speed: The injection speed must also be carefully controlled. A low speed can cause premature solidification of the metal in the mold, leading to defects in the part, while an excessively high speed may result in air pockets or surface imperfections.
3. Dwell Time Under Pressure
After injection, the piston holds the molten metal under pressure for a short period. This duration, known as “dwell time,” allows the metal to fill all the details of the mold before fully solidifying, eliminating potential defects.
- Dwell Time: This duration depends on several factors, such as the type of metal, the thickness of the part, and the complexity of the mold, and typically ranges from a few seconds to several tens of seconds.
4. Cooling and Solidification of the Metal
After the dwell time is complete, the metal begins to cool and solidify inside the mold. A cooling system integrated into the mold helps control the mold’s temperature, ensuring the metal cools uniformly. This is crucial for preventing thermal cracks or distortion in the final part.
5. Mold Opening and Part Ejection
Once the metal has fully solidified, the mold is opened, and the final part is removed from the mold using ejection systems, such as mechanical arms. This stage must be carried out carefully to avoid damaging the part.
Key Tips for Success in the Die Casting Injection Stage
- Precise Temperature and Pressure Control: Controlling temperature and pressure throughout all stages of injection is of utmost importance. This control ensures that parts are produced without defects and with high precision.
- Optimal Mold Design: The mold must be designed in a way that ensures the molten metal flows uniformly to all sections. This design can prevent defects such as air pockets or cold spots.
- Quality of Molten Metal: Using high-quality molten metal free of impurities plays a crucial role in producing high-quality parts. Impurities can lead to structural defects in the part.
Conclusion
The molten metal injection stage in the die-casting process is of particular importance and requires precise control over all its parameters. Attention to the details of this stage can lead to the production of high-quality, defect-free parts, which is critical in sensitive industries such as automotive and aerospace.